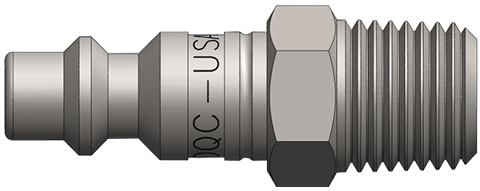
To put it plainly, quick disconnect couplings make your job easier. They are a fast and easy way to join pneumatic and fluid transfer lines by simplifying connections/disconnections and preventing air or fluid leakage. Pneumatic quick disconnects are used primarily to change between various tools, connecting the power source (compressor) to the tool. The system consists of two parts: the coupler (the female part) and the plug (the male part). Pneumatic couplings typically have a valve in the female half that shuts off the air supply automatically as soon as it is disconnected from a component ensuring the system stays pressurized.
Ah, but things aren’t quite that simple. Before using a quick disconnect system, there are a few questions you must address first: How do you identify the various types of pneumatic quick disconnect profiles? And how do you choose the correct quick disconnect coupling for the job at hand?
The Five to Remember
Pneumatic quick disconnect couplings typically fall into one of five basic profiles:
1. Industrial (Dixon DF-Series)
2. Automotive (Dixon J-Series)
3. ARO (Dixon M-Series)
4. Lincoln (Dixon L-Series)
5. European (Dixon CJ-Series)
Of the five, industrial quick disconnect couplings are the most common, while automotive is typically the second-most common. There is very little difference in performance or longevity between the styles. It is just a matter of preference. The main consideration is that the two styles are not interchangeable with one another. The most common frustration for people is when they have existing air couplers and they purchase the wrong style.
ARO, also known as Milton A-style couplings, are used on pneumatic lines in construction and factory automation. Lincoln-style quick disconnect couplings have a thin, smokestack-style stem, reminiscent of the 16th president’s trademark hat. The European standard is the most used pneumatic quick disconnect in Europe and features a high-flow inner diameter and valve design.
Most pneumatic quick-disconnect couplings have similar connections and features:
• Locking balls or pins that fit into place with a groove in the coupler plug which engages a seal.
• A sliding sleeve that releases the locking balls when it is retracted, permitting the plug to be inserted or removed.
• The coupler sleeve automatically returns to the locked position when released.
• An automatic shutoff valve in the coupler seals instantly when uncoupling, eliminating the need for a separate shutoff.
How to I.D. a Quick Disconnect
So how do you tell the various styles of quick disconnects apart? It’s not always easy. “It’s a very common error for someone to choose the wrong style for what they are already using in the application,” says Doug Exner, sales manager for Dixon. “For instance, choosing an automotive when you really need an industrial. The second most common error is choosing the wrong body size.
To avoid these errors, first, examine the shape of the plug. What does its profile look like? Compare your plug with a chart of quick disconnect styles and types. Following are several Dixon series profiles.
Industrial Interchange – Dixon DF-Series
Automotive – Dixon J-Series
ARO – Dixon M-Series
Lincoln – Dixon L-Series
European – Dixon CJ-Series
Next, you’ll need to determine the correct body size by measuring the diameter and tip length of the plug.
Dixon DF-Series pneumatic profile
Finally, you’ll need to know the thread or end configuration size since each series/body size has different end configurations.
As Exner says, “Each coupling style has different nominal body sizes that are matched to the hose size. A 1/4” body size coupling would be used with a 1/4” hose. A 3/8” and so on. That's the best practice for getting the best flow rate. Getting the right body size is important. If you have a 1/2” hose and try using a 1/4” coupling, you’re restricting the flow too much. You’re stepping down. The thread size will be specific to the hose. If it’s a 1/4” hose, it might still have a 3/8” thread, so it’s important to get the right size so it fits the hose or tool you’re working with.”
Choosing the Correct Quick Disconnect for the Job
So, which pneumatic quick disconnect coupling is right for your application? Consider the following before you decide:
1. Consider the environment
Is your job site in a potentially corrosive environment? Will you be working around chemicals or constant exposure to water? If so, stainless steel couplings are the way to go. If you require higher pressure, choose carbon steel, which provides better pressure performance than brass.
2. Consider the profile
Industrial? Automotive? ARO? Which profile you choose has more to do with which profile you are already using. It’s helpful to stay consistent in any work environment. If most of your quick disconnects are industrial, stick with that profile when choosing new parts.
3. Choose a size
The size will be determined by the diameter of the hose and the port size on the tool. Make sure to double-check both before choosing a quick disconnect!
Safety Concerns
All quick disconnect couplings should be viewed as potential hazards that can cause property damage or personal injury if used or installed improperly. Improper use includes selecting a product unsuitable for your application, installing or using the product incorrectly, and/or ignoring signs of imminent failure or misuse.
Read over the S.T.A.M.P.E.D. checklist:
Also, it’s a good idea to always buffer the coupling from the tool with a 6- to 12-inch-long whip hose to absorb and dampen any vibration. “When the coupling is threaded directly into the tool, that coupling is taking the brunt of the energy the tool is giving off and can destroy the coupling or significantly shorten its lifespan,” says Exner. “A tool giving off any vibration can damage a 1/4" coupling if it's installed directly into the tool just as much as a 3/4" coupling in an outside air application. Using a whip hose is best practice with any tool or equipment, regardless of size."
To learn more about how to select the proper pneumatic quick disconnect coupling for your application, talk to a product specialist at 877.963.4966 or visit dixonvalve.com