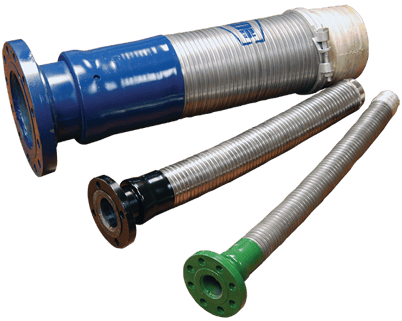
An old proverb says necessity is the mother of invention. When an important need or problem arises and presents obstacles, we are challenged to create a solution. In a nutshell, this is how Dixon's GSM Armored Hose came about.
History
In the 1800s, the Bessemer process, open-hearth furnace, and electric furnace were the most commonly used steel production methods. In 1948, the basic oxygen furnace (BOF) was invented, and by 1953 it was commercialized to speed up the steelmaking process.
The Problem
Each of the aforementioned extraction and refinement processes had challenges, but they all shared one important commonality. They all required strong, safe equipment to withstand the heat, corrosion, and abrasion of producing iron and steel.
Prior to the development of the BOF, Howard W. Goodall, the founder of Dixon, was operating the Goodall Rubber Company. The company was designing and manufacturing Goodall Semi-Metallic (GSM) oxygen hose for the open-hearth process, and GSM furnace door hose to carry water to cool the open hearth doors. Although the company was sold in 1924, the GSM product line continued to be made. In 1964, a major steel company challenged the Dixon engineers to develop a hose to handle oxygen and water in the BOF process.
At the time, flexible hoses made of all metal were typically used. However, as these hoses flexed and moved, the packing between the metal joints eventually failed and oxygen leaked. This may not seem like a major concern, but when you consider the flammability of oxygen and the 3000°F (1649°C) environment it was released in, the safety hazard becomes obvious. Additionally, the leak created technical problems as the amount of oxygen delivered was less than what was needed for the process to function properly, which increased production time and reduced efficiency.
Furthermore, the metal hoses and their movement added unnecessary noise to an already loud environment. The steel company's goal was to adapt the qualities of the other two GSM hoses to create a third hose specifically for BOFs. Although Dixon had only previously manufactured GSM hoses with a 4-inch I.D., the company was up for the challenge to create a 6-inch I.D. GSM hose.
The Solution
Six months later, 63 feet of 6-inch GSM-BOF hose was ready for the steel mill. The new hose featured the basic GSM design with modifications. The hose was made of a neoprene tube, which does not react chemically to oxygen, and featured a braided carcass with helix wire reinforcement. The outer cover was armored steel in a ball-joint configuration to combine strength, flexibility, and resistance to heat. Special couplings were also engineered to anchor the wire without damaging the carcass or tube.
The GSM Armored Hose was used with the BOF for 2-1/2 years without any issues. At that time, it was inspected and showed no evidence of wear or deterioration inside. Only the exterior exhibited signs of the hard service it was exposed to daily. This was a dramatic improvement from the previously used all-metal hoses that had to be replaced several times a year.
Application, Construction, and Features
The armor on GSM Armored Hose is constructed of galvanized or stainless steel and is available in a wide selection of inner hose materials specific to the demands of the application. The extremely flexible ball-joint armor protects the hose from heat, molten splash, and abrasion. Multiple layers of fiberglass insulation are applied for heat resistance up to 1000°F (538°C). The inner hoses, engineered for the application, are specialty industrial rubber, hydraulic, corrugated stainless steel, or PTFE. There are no interlocking parts to restrict bending, and the half-round wire ball joint design allows multiple plane movements while providing resistance to kinking.
Buck Foundry
Although GSM Armored Hose was originally created for steel mills, foundries have benefitted from the product, as well.
Buck Foundry, located in Quarryville, Pennsylvania, creates ferrous and non-ferrous metal castings. Buck made a significant investment in its operation with the purchase of a new auto-pouring furnace. Typically, foundry furnaces are outfitted with basic rubber hoses, which can burn up easily. These hoses work fine until something goes wrong.
Unfortunately for Buck, something did go wrong. An unexpected leak of molten metal burnt the hydraulic and water lines attached to the new piece of equipment, costing significant downtime and money. Buck turned to Dixon Specialty Products for help. The company decided to invest in GSM Ball-Joint Armored and Insulated Hoses to avoid another disaster. The equipment, outfitted with GSM Armored Hose, was ready to withstand the elements.
"That GSM hose saved the day and us a lot of money in repairs," said Jim Kundratic, Buck Foundry Executive Vice President.
Reasons to Use GSM Armored Hose
GSM Armored Hose is beneficial for a variety of reasons, including cost, longevity, and durability.
While GSM Armored Hose is a larger investment, it saves significantly in terms of downtime and long-term operation. In the Buck example described above, when the hydraulic and water lines were burnt they were down for months. By switching to GSM Armored Hose, Buck saved $500,000 in repairs and $500,000 on production not being lost, resulting in an overall cost savings of $1,000,000.
"At some point, it makes sense to outfit all of our furnaces with GSM Armored and Insulated Hoses," said Brad Harris, Buck Foundry Maintenance Manager.
In terms of longevity and durability, GSM Armored Hose was specifically designed to withstand the extreme environments found in steel mills, foundries, etc. The multiple layers of insulation completely encase the inner hose for maximum heat diffusion, while the continuous heavy gauge wire construction ensures resistance to impact and abrasion. GSM Armored Hose is fit for high heat and abrasive applications, so it holds up longer than standard rubber hose in these environments, making it a reliable, long-lasting choice.
Summary
Dixon's commitment to innovation can be traced back to our roots in the Goodall Rubber Company with the development of the GSM Armored Hose. What started as a challenge from the steel processing industry has transformed into a successful product that meets the demanding needs of a range of applications. When we say we strive to provide real solutions for real challenges, we mean it.
Dixon offers a variety of GSM Armored Hose assembly options. To create The Right Connection® for your specific application, visit dixonvalve.com or contact Dixon Specialty Products at 888.226.4673.