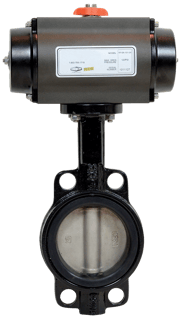
So, what is an actuated valve? An actuator is a mechanism that controls the positioning of the valve mechanically versus manually. These actuators are critical for ensuring that process control is automated in a consistent manner.
Pneumatic actuators and electrical actuators are the two most prevalent forms of actuators. Enhanced manufacturing speeds, improved safety procedures, and cheaper maintenance costs are some of the additional advantages of these valve actuators.
Actuated valves are used in several industries including:
- Oil and Gas
- Paper and Pulp
- Mining
- Water and Wastewater
- Food and Beverage
- Energy and Power
- Automotive
Types of Actuators:
Pneumatically actuated wafer and lug style butterfly valve
Pneumatic Actuators:
Dixon’s pneumatic actuators are utilized in a variety of valve control procedures to regulate flow as well as control pressure. Pneumatic valve actuators generate motion by converting air pressure. The device applies an air force to a diaphragm, rotary vane, or piston linked to the actuator shaft, which is then mechanically coupled to the valve or damper stem. Pneumatic actuators can generate either linear or rotational motion, depending on the kind.
Advantages of Pneumatic Actuators:
- Easy to install
- Long-lasting and dependable
- Cost-effective
- Low maintenance
- Air pressure can be stored, allowing the valves to be used when power is lost
- Great for repetitive opening and closing of valves
- Used when electrical actuation is not safe (hazards/fire)
Electrically actuated 3-piece ball valve
Electric Actuators:
Dixon’s electric actuators provide rotational motion and function with several valve types, including ball and butterfly valves. Electric valve actuators respond to commands through remote control or centralized process control systems, making them important for controlling systems that are difficult to access or distributed across a vast region. Process control systems can use a centralized system to manage electric actuators and provide planned and programmed commands, allowing companies to automate the system and increase dependability. In the case of an emergency, a lever or a handwheel can be used to override the system.
Advantages of Electric Actuators:
- Silent
- Low-energy consumption
- Provides the highest level of accuracy
- Simple to program
- Provide complete movement control
- Allows you to control with 12VDC, 24VDC, 24VAC, 110VAC, and 220VAC
What is the most suitable actuator for your requirements?
When choosing an actuator for a valve, various things must be considered to ensure that the appropriate actuation technique (and size) is chosen for the application. Although each actuator has its own set of benefits, selecting the correct one for your application is based on several factors such as the power source, speed, number of cycles, size, temperature range, and areas.
Power Source:
The power source is the most important factor in determining the type of actuator. Electric is the way to go if there is no air available.
Time and Speed:
The turning speed of a pneumatic actuator is immediate, but an electric actuator takes an average of 25 seconds to spin 90 degrees.
Cycles:
The pneumatic actuator can cycle as many times as you like. The electric actuator, on the other hand, is slower and has a limit on the number of cycles it can do in a period of time.
Size:
While pneumatic actuators can deliver high torques, the higher the torque, the larger the rack and pinion actuator. Electric actuators enhance torque by altering the gear ratio, allowing for higher torques in a compact size.
Temperature Range:
Pneumatic actuators can function in temperatures ranging from -4 to 150°F (-20 to 70°C) and, in certain circumstances, -40 to 250°F (-40 to 121°C) if the proper seals, lubricant, and bearings are used. Electric actuators can operate in temperatures ranging from -40 to 150 °F (-40 to 65°C).
Hazardous Areas:
Pneumatic actuators are generally favored in hazardous or toxic settings owing to their explosion-proof nature, although electric actuators can be utilized if compressed air is unavailable or if a pneumatic actuator fails to fulfill other operational criteria. Electric actuators used in hazardous settings must be protected from explosions by a NEMA VII enclosure.
In conclusion, actuators are vital to the success of process control across numerous industries. If you have any questions when selecting a method of actuation, please contact a Dixon specialist at 877.963.4966.
If you enjoyed the article, please share it with your colleagues!