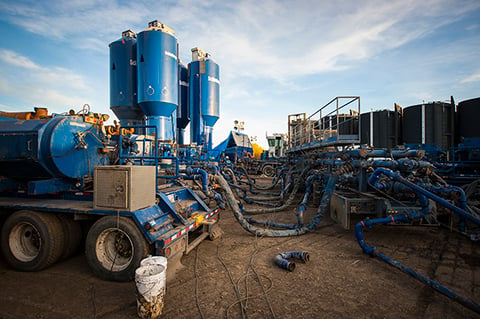
What do cars, houses, deodorant, and MRI machines have in common? They all use oil or natural gas. While it’s commonly understood that we use gasoline made from oil to fuel vehicles, and natural gas provides heat for homes and businesses, the extent to which we depend on oil and gas in our everyday lives is often overlooked. Since society is dependent on the exploration and production of petroleum and natural gas, it is important for the extraction process to be cost-efficient and effective. Hydraulic fracturing is helping to meet these objectives.
The increased accuracy of geo-locating and mapping oil reserves, the perfection of horizontal drilling, and the evolution of frac fluid/proppant (water, sand, and chemicals) have made hydraulic fracturing a lucrative business. To support the continued demand for energy while remaining profitable and promoting environmental stewardship, equipment operators, manufacturers, and well owners are working to develop alternatives for hydraulic fracturing equipment.
Aerial view of a natural gas well being drilled in northwestern West Virginia in the Marcellus Shale formation.; Photo courtesy of iStock/6381380
History and Overview
The development of modern hydraulic fracturing, also known as fracking, is rooted in 1865 when Colonel Edward Roberts' "exploding torpedo" was lowered into an oil well and detonated. Less than 100 years later, in the 1940s, explosives were replaced with high-pressure blasts of liquid.
Today, hydraulic fracturing extracts oil and gas from the earth using a frac fluid mixture of water, sand, and chemicals. High pressure is used to blast the mixture below the earth's surface and create fractures. The water in the frac fluid is used to further crack and break down the rock. The sand gets wedged in the fine cracks to keep everything open for extraction, allowing previously trapped gas and oil to flow to the surface.
Hydraulic fracturing or fracking site at Dawson Creek, Canada; Photo courtesy of iStock/MajaPhoto
Options for Powering Hydraulic Fracturing Equipment
Modern hydraulic fracturing involves the use of heavy-duty equipment for extraction. This equipment can be powered in different ways, including diesel, natural gas, and dual fuel.
Diesel
Diesel-powered engines are the traditional power source for hydraulic fracturing operations. A diesel-powered machine called a blender combines the sand, water, and chemicals and then pumps the mixture into the low-pressure manifold. From there, the frac pumps pressurize the frac fluid and send it down the high-pressure line into the hole for fracking.
Typically, an automated remote monitoring and fueling system is utilized, which allows the fuel hoses to provide the blender and frac pump engines with a constant supply of diesel to keep the system running until the well sections are completed. This prevents fracking operations from pausing to manually refuel.
There are several advantages to using diesel fuel to power fracking operations. Diesel engines are known, readily available, and powerful, making them effective and efficient at fueling fracturing equipment. The drawback, though, is the potentially high operating cost due to the fluctuation of diesel prices.
Natural Gas
Natural gas is another option for powering hydraulic fracturing equipment. The two most common options for natural gas operations are electric fracking and direct drive.
Electric fracking, also known as e-fracking, is similar to diesel-powered operations in terms of process, and semi-similar in terms of equipment. Electric fracking typically uses a single gas turbine to generate electricity to power multiple motors. The motors replace the diesel engines located on each frac pump and blender. Instead of fuel lines to the blender and frac pumps, there are electrical lines from the generator to each of the electric motors.
With direct drive, the blender and frac pumps are individually equipped with a gas turbine directly connected to their pressure-generating system. With e-fracking, losing the gas turbine means losing power completely. Direct drive, however, can continue operation even if one turbine loses power. Additionally, e-fracking and direct drive equipment typically offer similar or more fracking horsepower over a smaller footprint. This allows for fracking operations in space-constrained areas.
Using natural gas as the fuel source for fracking is advantageous because it is readily available at a lower cost compared to diesel and requires fewer personnel for operation. This reduces operating costs. Natural gas also burns cleaner with lower CO2 and nitrogen oxide (NOx) emissions, no sulfur oxides (SOx), and no particulates from the exhaust. You can learn more about NOx and SOx in our Liquefied Natural Gas: The Fuel of the Future for Shipping and Transport whitepaper.
Most of the hydraulic fracturing industry still uses diesel-powered equipment, so it is expensive to convert current operations to run on natural gas. Additionally, field gas isn't always compatible straight from the well. The natural gas may contain water, CO2, or hydrogen sulfide (H2S), which contaminates the gas for use as a fracturing fuel source. Additional equipment is needed to condition the field gas to be used by engines or turbines.
Dual Fuel
The third option for powering hydraulic fracturing equipment is dual fuel. Also called bi-fuel, these engines can operate on a mixture of two fuels, typically diesel and natural gas. Hydraulic fracturing operations using dual-fuel engines are similar to diesel-powered operations, but they include a natural gas line coming from trucks or a well. Dual-fuel engines can also operate solely on diesel if natural gas is temporarily unavailable.
The use of dual fuel in hydraulic fracturing operations is advantageous both environmentally and financially. From an environmental standpoint, less diesel is required for operation, which reduces diesel refining and transportation. The use of dual fuel offers the power and efficiency of diesel fuel with less environmental impact.
In terms of finances, dual fuel is beneficial because diesel typically has to travel a long distance to reach the engine on-site. Each step of transportation is an added cost. Conversely, natural gas is produced at a wellhead and can be processed and delivered on location. Natural gas is plentiful in the U.S., so it is often priced lower than diesel when compared according to its energy density. Supplementing diesel fuel with natural gas reduces diesel consumption and overall costs. In addition, purchasing a dual-fuel kit to convert an existing diesel operation is cheaper than buying new diesel equipment.
Dual fuel has its challenges, too. Adequate supply and access to both diesel and natural gas are required for dual-fuel operations. Also, current operations powered strictly by diesel or natural gas cannot start using dual fuel without converting equipment. Converting diesel engines to run on dual fuel requires time and money, which is an added cost.
The use of dual fuel is a cleaner solution to diesel and an intermediate step in the right direction to get to 100% renewable energy and helps the oil and gas industry reduce its carbon footprint.
The Right Connection® for Hydraulic Fracturing
Dixon® plays an integral role in supporting the various fueling options for hydraulic fracturing. Our engineering expertise, world-class customer service, and wide product offerings cover the full spectrum of natural gas and diesel connections.
Dixon MannTek Dry Gas Products
Dixon MannTek Dry Gas Adapter Tank Unit x Female NPT
Dixon MannTek Dry Gas Adapter Tank Unit x 150# ASA Flange
Dixon MannTek Dry Gas Coupler Hose Unit x Female NPT
Features:
- Quick and easy to connect, it can be connected to a unit with pressures up to 225 PSI (maximum 360 PSI)
- For higher pressure, couplings can easily be equipped with a pressure relief valve that dissipates trapped fluid pressure into the hose coupler without spillage
- Reliable - easy to use, easy to maintain, and saves time
- Minimizes the risk of cold burns, spillage, and product loss, and health risks
- Keeps the environment free of hazardous vapors and liquids

Dixon MannTek Dry Disconnect Products
Dry Disconnect Adapters
Dry Disconnect Coupler
Features:
Easy to handle - push and turn - free flow, turn and pull - closed
- Time-saving - no need to drain hoses or pipe systems
- Economical - no loss or spillage of liquids at connection or disconnection
- Safety - the valve cannot be opened until the unit is coupled
- Environmental friendly - accidental spillage eliminated when properly used
- Safe and reliable - due to rugged construction
- Product life - uncomplicated design and high-quality materials ensure long product life
- Selectivity - to avoid product contamination, selective versions of the couplers and adapters are available. Contact Dixon for further information.
CNG-series
Features:
- Meets CNG service requirements
- Improved body and valve design provides a 30% increased flow performance over standard ISO-B designs
- Latch mechanism provides brinelling resistance
- Locking sleeve design prevents accidental disconnection
- Captured valve O-ring for reliability in high-flow conditions
- CNG plugs supplied with a combination dust cap/plug
- Non-sparking material
Other related connections for hydraulic fracturing operations include Cryogenic Products, FloMax Fluid Management Systems, and Bayloc Dry Disconnects.
Summary
In recent years, the oil and gas industry has sought technological advances in frac equipment that sustains hydraulic fracturing as a viable extraction process in support of energy policies while promoting environmental stewardship. This inspired the transition from strictly diesel-powered hydraulic fracturing equipment to the development of natural gas and dual-fuel alternatives. All three fueling options are effective at extracting crude oil and natural gas from the earth with pros and cons to each. As a result, the fueling system used at each frac site varies, which means the connections required for each operation also differ. Dixon is delighted to provide a wide range of products to meet the needs of diesel, natural gas, and dual-fuel-powered fracking operations. We are committed to providing The Right Connection® for every application.
If you have any questions, please contact a Dixon specialist.