The hottest area in a steel mill is inside and around the furnace. Whether the furnace is a basic oxygen furnace (BOF) or an electric arc furnace (EAF), its surrounding area is extremely hot. The temperature required to melt the raw materials of steel is in excess of 2,750 degrees F (1,510 degrees C).
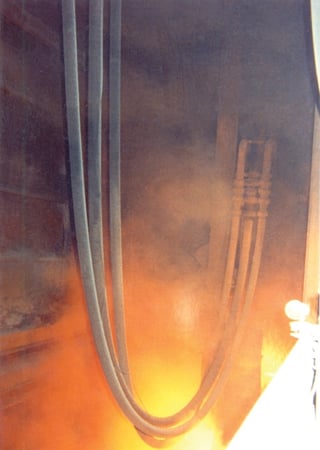
During the steelmaking process, raw materials are added to the furnace to create the proper chemistry required. Iron ore, carbon, silicon, manganese, phosphorous, sulfur, nitrogen, boron, chromium, molybdenum and scrap are all possible additives to the mix. As the furnace roof is moved out of the way, these products are added. The resulting reaction causes a shower of hot sparks, scrap, slag and “skulls” to fly from the furnace—landing on surfaces around the furnace, including hose assemblies. It’s quite a sight to see.
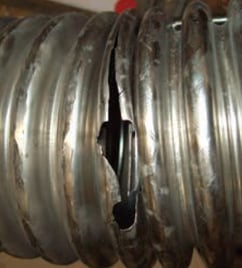
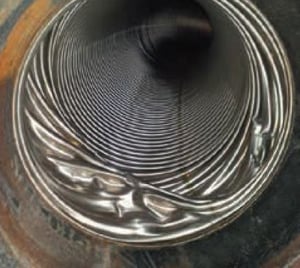
Image on the left: Metal hose liners rupture from impulse cycles created by vacuum pumps when pulling spent water throughout the cooling system. Image on the right: When using metal hose or un-protected rubber hose with swivel joints, severe hose twists can occur, restricting water and eventually causing shut-down to an EAF.
Because of the high ambient temperature and the hot flying sparks, the surrounding hose assemblies (including furnace and roof cooling water, oxygen and hydraulic assemblies) are subjected to extremely high temperatures and need to be protected.
The heat and falling slag aren’t the only stressful conditions impacting the hose. Assemblies are also subjected to movement during the unloading of the molten steel. The furnace roof swings out of the way of the tilting furnace, cooling lines are lifted free, and hydraulic lines are moved by the action on the furnace. The heat and movement of this application affect the life expectancy of each assembly, limiting the lifespan of each one to between 10 months and three years. Hydraulic assemblies may last only weeks, depending on the number of “heats” (conditions) endured.
A mill’s acquisition price is only a portion of the total cost required to remove and replace large bore furnace hoses. Other related costs/ activities include:
- time required to move these large assemblies from storeroom to melt shop
- staging of necessary lifting equipment
- scheduling of mechanical teams for the change-out
- review of proper safety procedures, i.e. lock-out, tag-out, fall protection
- ensuring that all personnel have proper safety clothing and equipment
- limiting production downtime to a minimum (Hose change time can range from 30 minutes to six hours, and typical downtime costs can range from $130 to more than $600 per minute.)
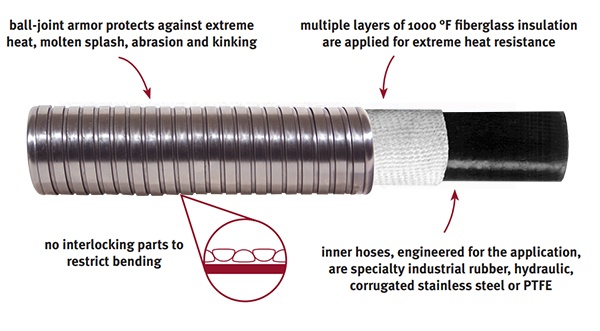
A Cool Solution: Dixon has been fabricating and supplying GSM Ball Joint Armored hose assemblies for water-cooling, oxygen and hydraulic transfer applications in steel mills for more than 50 years. The unique half-round design not only prevents hose kinks, but also keeps the hose round for continuous and consistent flow of media around the furnace crucible and roof panels. Ball joint armor can be applied to hose sizes ¼-inch through 12-inch ID.
In addition to the GSM Ball Joint Armor, Dixon can also apply one or more layers of 1,000 degrees F-fiberglass insulation between the hose cover and the GSM Ball Joint Armor. This insulation gives even more heat resistance and longer life to whatever type of hose it is applied.
DIXON GSM BALL JOINT ARMOR AND INSULATION ADVANTAGES:
- protects hose from excessive heat
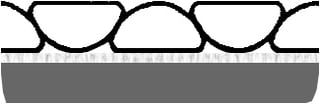
- protects hose from abrasion
- protects hose from hot partials landing
- protects hose from kinking
- protects hose from crushing
- protects hose from twisting
- protects hose assemblies
Turn to Dixon today to apply genuine GSM Ball Joint Armor to protect your hose from excessive heat, abrasion and metal braid or rubber cover abuse.