Manufacturing is a fast-paced environment where every company faces the challenge to ramp up production as demand increases. The challenge becomes critically important in the food and beverage industry where complying with Food and Drug Administration standards while increasing production is a necessity. There are many ways to help production meet demand; adding people, extra shifts, and equipment to name a few.
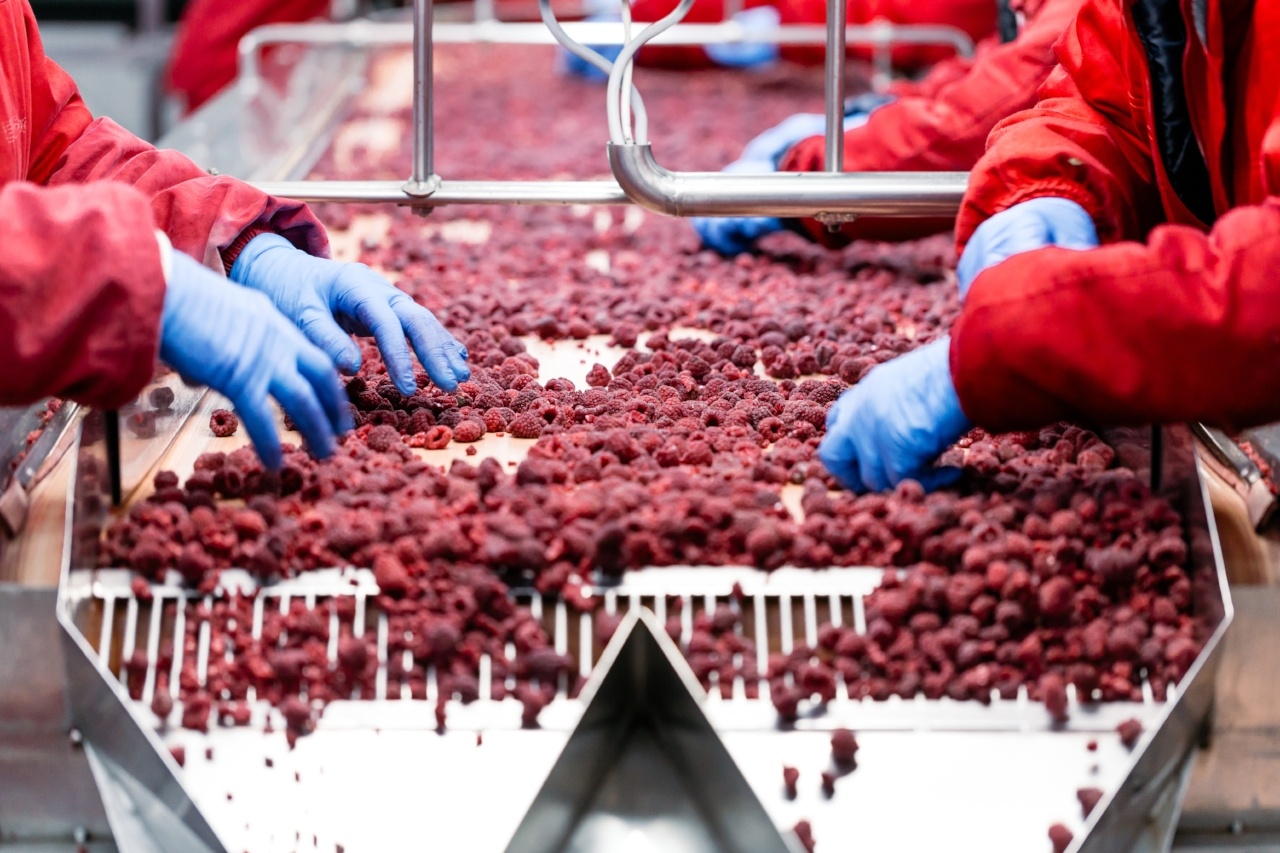
At a plant producing edible goods, the finish process line must be cleaned at predetermined intervals or when the process is complete. Two methods are commonly used for cleaning. The Clean In Place (CIP) method runs a hot soapy solution through the system with all components, including hoses, in place, followed by a hot water rinse. In the Clean Out of Place (COP) system all the component pieces are removed and cleaned in a wash tank or with steam.
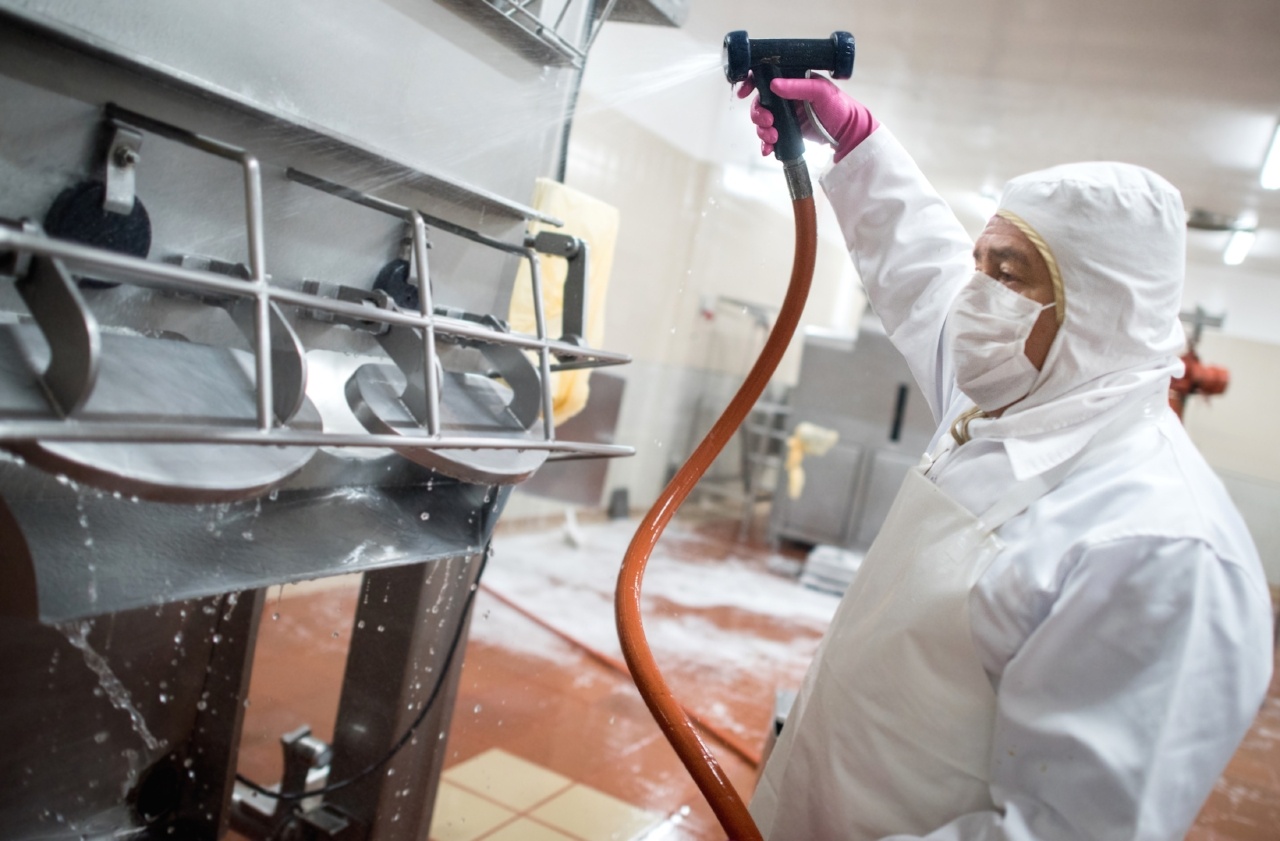
Occasionally newly added start-up shifts are understaffed and overwhelmed with the task of keeping all the components in a hose assembly in excellent operating condition. In one instance where workers were instructed to replace a failed hose assembly, there was no replacement assembly to be found in the storeroom. Workers did uncover couplings that had the same connection as those on the failed assembly and further searching uncovered clamps they had seen in other parts of the plant and a tool to install them. Under pressure to get production up and running, and assuming one coupling is the same as another, they replaced the leaking coupling with the “new” ones they had found. The repaired assembly was put in place, the valves opened and production resumed.
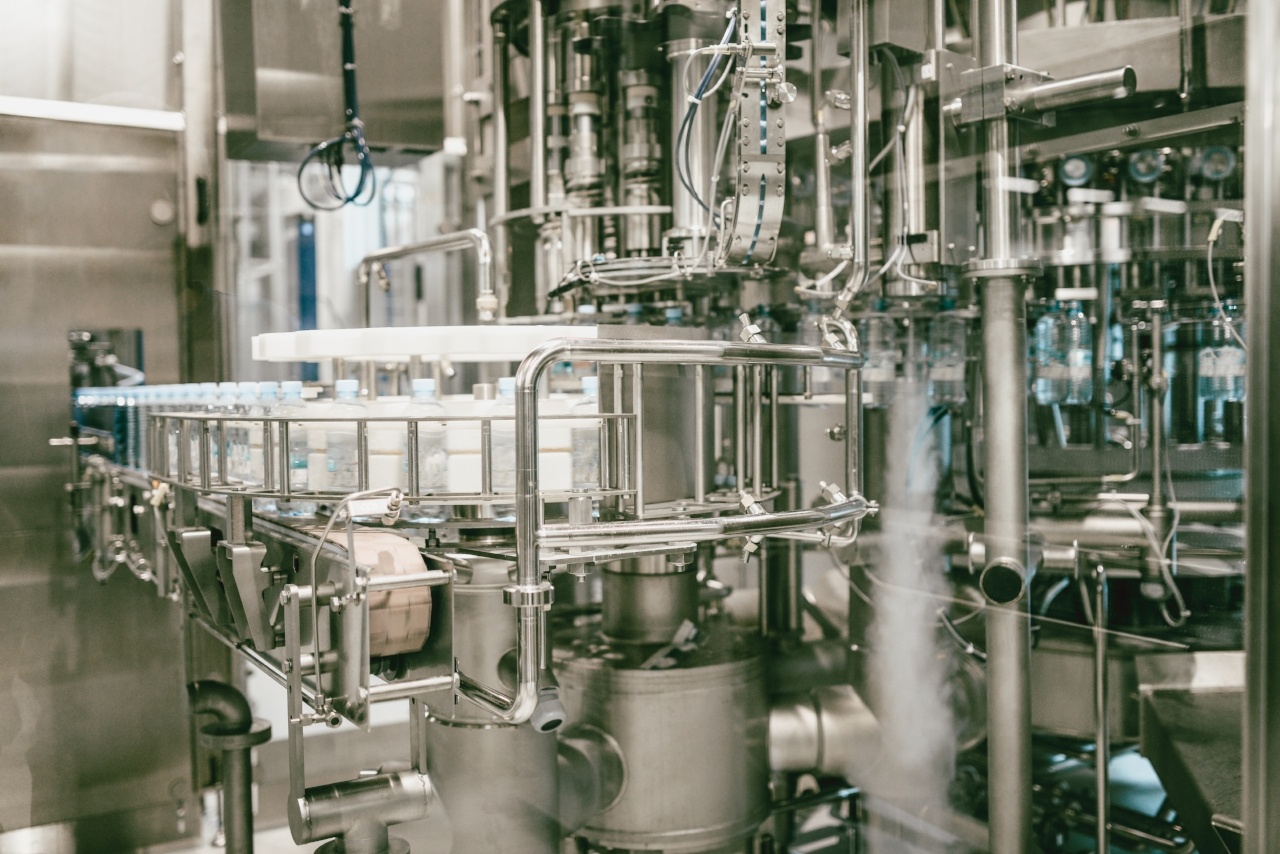
Later, during routine testing, quality control found unusually high bacteria counts in samples taken from the packaging line. Production stopped immediately, national product recalls were issued, and an emergency meeting was called. After hearing about the repair made a few weeks prior, it was discovered the replacement coupling, with a traditional shank, did not conform to Food and Drug Administration standards for sanitary couplings. Even though all CIP cleaning and sanitary procedures were followed this replacement assembly was put into service, and bacteria propagated at the end of the shank and contaminated a vast quantity of product.
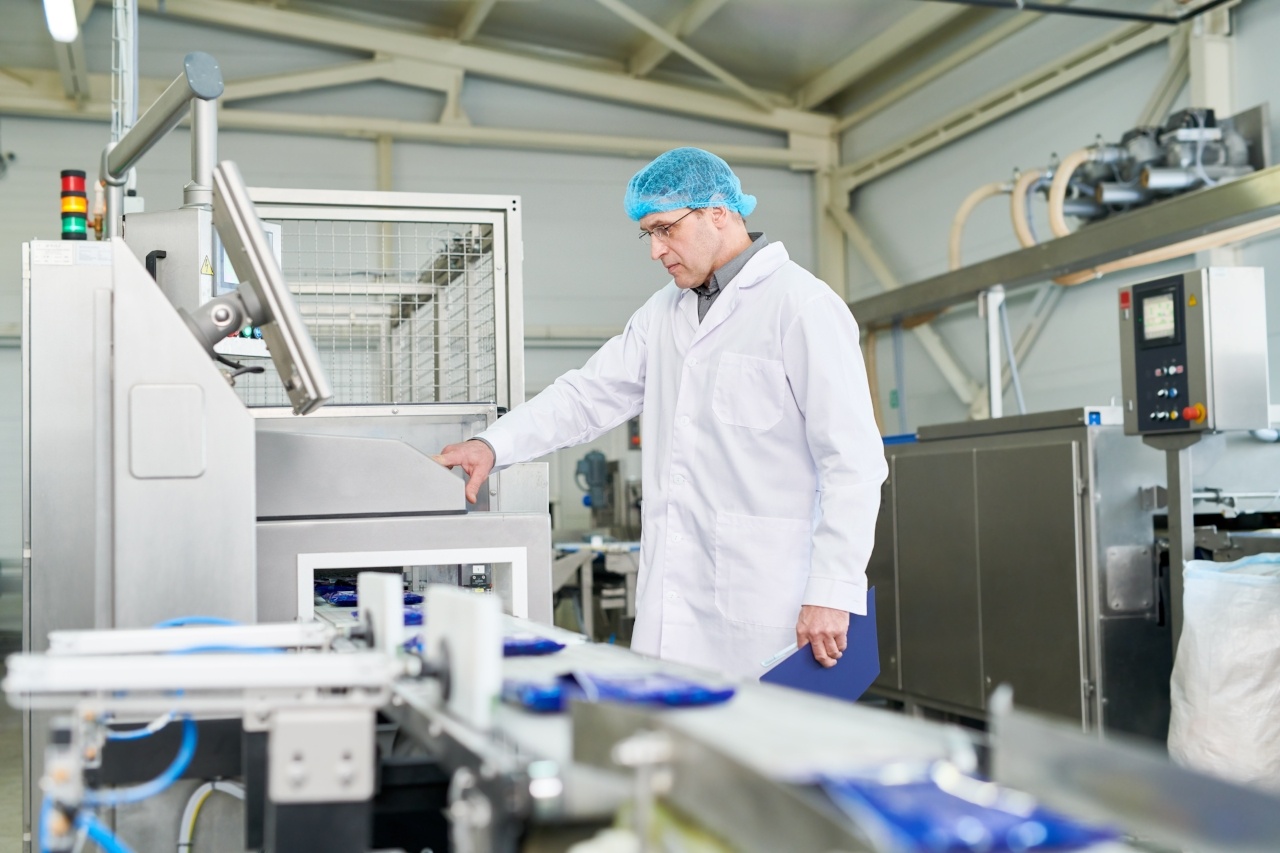
The ability to improvise is a great human trait but improvisation for hose assemblies is not advised and can be costly. Couplings and retention devices are designed to work safely for their intended use. The selection of the proper hose, coupling, and retention device, and the proper application of the coupling to the hose are of utmost importance.
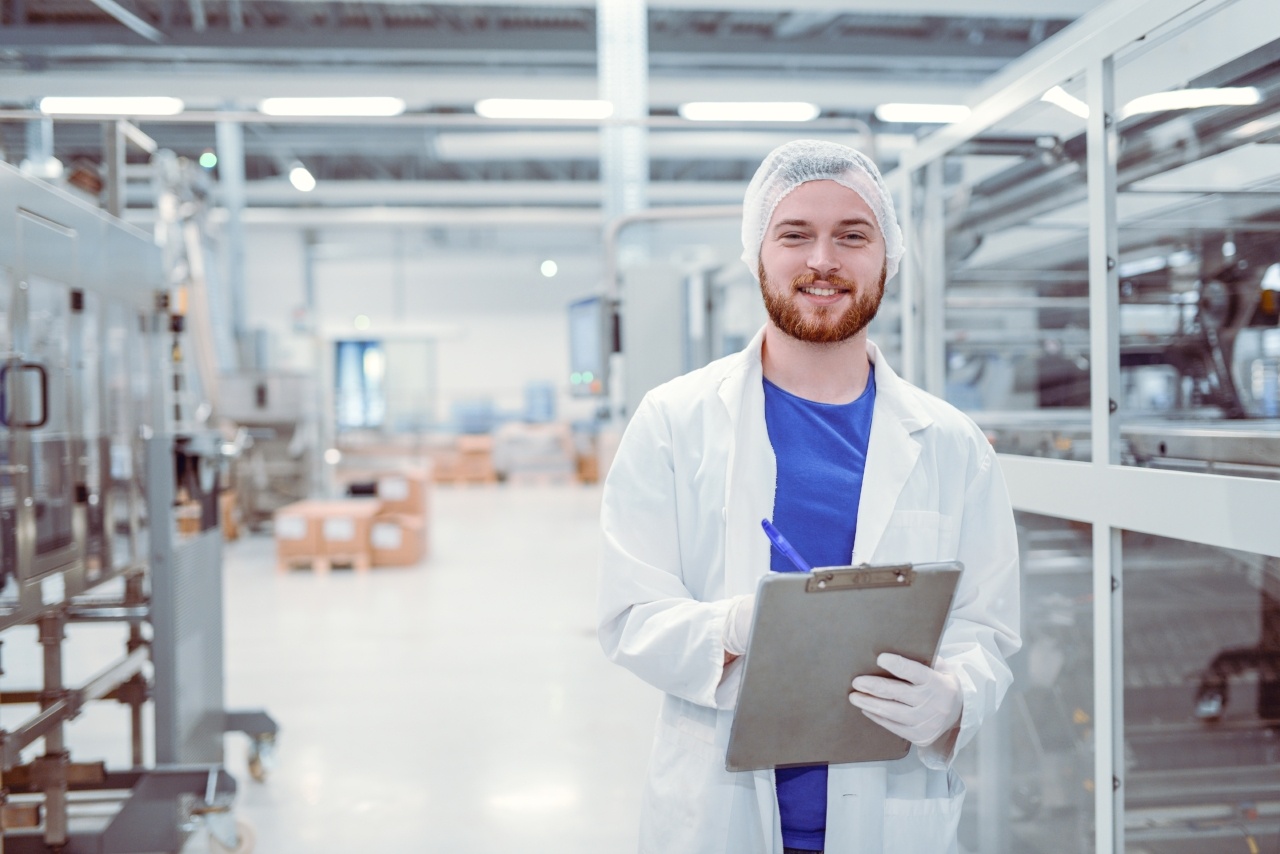
Users must consider the size, temperature, application, media, pressure, and hose and coupling manufacturer's recommendations when selecting the proper hose assembly components. Dixon recommends that all hose assemblies be tested in accordance with the Association for Rubber Products Manufacturer's (ARPM) recommendations and be inspected regularly (before each use) to ensure that they are not damaged or have become loose. Dixon is available to consult, train and recommend the proper selection and application of all fittings we sell, to make use of this service call 877.963.4966 or email sales@dixonvalve.com.