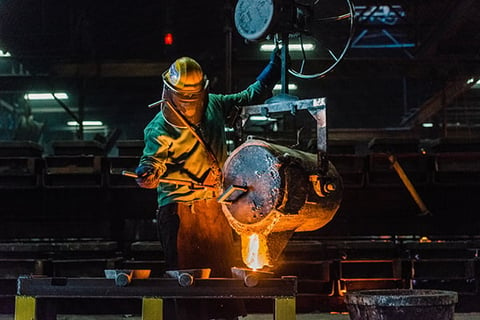
The origins of metal casting date back at least 5,000 years. However, the process has evolved considerably over the years with the discovery of different metals and the advancement of technology. At Dixon®, we use two main casting methods to create metal parts; sand casting and investment casting. Though both processes include pouring molten metal into a mold to create metal parts, there are significant differences between them. Keep reading to learn about these casting processes and their differences.
What is Sand Casting?
If you've ever made a sandcastle at the beach, you know that sand can be used to mold detailed shapes. The sand casting process isn’t much different. Using sand molds, manufacturers can create metal parts of all sizes, ranging from a few ounces to several tons.
To create sand mold casts, hollows are made in moistened sand, filled with molten metal, and left to cool. Because of its flexibility, heat resistance, and relatively low cost, sand casting is the most widely used casting process.
Metal pourer discarding his/her excess metal from the pouring ladle into the "pig iron" trough at Buck Foundry in Quarryville, PA. This will be reused when melting another furnace.
How Does Sand Casting Work?
The process has six main steps:
- Place the pattern in the sand. The pattern is generally made from aluminum and should look like the outside of the part you are casting.
- Set up a gating system. The gating system is a series of passageways that allow the molten metal to get into the cavities created by the pattern.
- The pattern, which has two halves, is removed from the sand. The sand is packed around both halves in what looks like a big box. After the sand is packed around the pattern, the pattern is removed, and both halves of the box are assembled.
- Pour molten metal into the mold; it runs the gate system to the cavities you created with the pattern.
- Let the metal cool and then break apart the mold and remove the casting.
- Lastly, it goes through a finishing process of removing the gate and cleaning up the casting.
Employee "racking" (refers to the process of cleaning excess sand off cores and placing them on a rack) cores in the core room at Buck Foundry. This helps ensure the core is to the proper dimensions.
What is Investment Casting?
Investment casting is used to produce components for spacecraft and jet engines — even for making dental crowns! For the investment casting process, manufacturers create a wax pattern to create the void for producing metal parts. The ceramic shell is built around the wax pattern, and when it is hard enough, manufacturers will remove the wax pattern from inside the shell. They then pour the molten metal into the shell and allow it to solidify. The final investment casting parts will have a smooth surface and the same shape as the wax pattern. The removed wax can be reused next time.
How Does Investment Casting Work?
The investment casting process has eight main steps:
- Make a mold out of aluminum. In this process, the aluminum is the mold instead of sand.
- Pour the wax into the mold. The wax cools and you remove it from the mold. The wax looks just like the part you are casting.
- The wax is attached to what is called a tree, and each individual wax part is attached to the wax tree.
- The wax tree is dipped into a series of ceramic slurries.
- The wax tree is put in a furnace to harden the ceramic, melt the wax, and remove it.
- The molten metal is poured into the ceramic shell.
- The metal cools and the ceramic shell is broken apart and the casting removed.
- Lastly, the casting goes through a similar finishing process as the sand casting.
Image courtesy of Forerunner 3D Printing
Why is it Called Investment Casting?
It’s clear how sand casting got its name, but what about investment casting? Well, it has nothing to do with finances. The term “invested” historically carries the meaning of “clothed” or “surrounded.” So, investment casting is so named because of the shell of ceramic, plaster, or plastic that is formed around the wax pattern.
What are the Main Differences Between Sand and Investment Casting?
Besides the different processes outlined above, sand castings are generally less expensive, have higher production volume, and have a less coarse surface finish. Sand castings have more variation from part to part and a higher tolerance, which generally results in more machining and more material. Investment castings are more expensive, offer lower tolerances, use less material, and generally look better.
Sand vs Investment Casting: A Quick Comparison
What are the Types of Metal Materials Used for Sand and Investment Casting?
The difference between sand and investment casting is also reflected in the metal material used. Manufacturers must consider metal material tolerance, melting point, and other features when selecting a casting method. Here are some examples of sand and investment casting material selections:
- Sand casting: iron, brass, and aluminum
- Investment casting: stainless-steel or Hastelloy
Which is Dixon's Preferred or More Used Process?
That depends on many factors. In general, Dixon uses sand casting for less expensive materials that are relatively easy to machine and are higher volume. Dixon uses investment casting for expensive materials that require higher machining cycle times. Investment casting can produce parts that are closer to near net shape meaning that the shape of the part, in this case, the casting, is close to finish dimensions. This means there is less material to machine off which cuts down on the length of time required to machine the castings. Both casting methods offer advantages and disadvantages. While designing our parts, we look at the cost-benefit ratio for each process and choose the one that offers the most value.
Watch this video to learn more about Buck Foundry. If you have any questions about sand or investment casting, reach out to one of our foundry specialists.