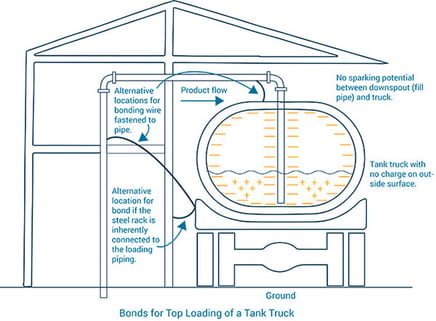
Have you ever gotten out of the car and reached for the door only to be met with a shock? The small zap, caused by static electricity, is alarming, but in this scenario it’s harmless. However, when it comes to tank trucks hauling petroleum and other highly flammable products, a static shock can spark a dangerous situation.
photo courtesy of iStock
Static Electricity
Every object has positive and negative electrical charges. These charges occur in pairs to stay balanced. When two materials make contact, electrons, the negative charges, move from one object to the other. When the objects separate, there is an imbalance of charges, which generates static electricity. In the example above, electricity is discharged across the gap between your hand and the car door because of the difference in electrical potential. The resulting shock is called static discharge.
In the petroleum industry, static electricity is a concern because of the contact and separation during the tank truck loading process. Initially, the liquid is electrically neutral. As the product moves through the pipe, negative charges build up on the walls and positive charges flow with the liquid, generating static electricity. The electrical charges on the two surfaces can accumulate enough energy to produce static discharge. The difference, however, is that the static discharge occurs as a spark capable of starting a fire.
Ignition
Three elements are required for a fire: fuel, air, and a source of ignition. For tank trucks, static sparking is the main source of ignition.
According to the American Petroleum Institute (API), four conditions must be present for static electricity to cause ignition:
- A means of generating a charge
- A means of accumulating a charge capable of producing a spark
- A spark gap
- An ignitable vapor-air mixture in the spark gap
Vapor-air Mixtures
The flammability of a vapor-air mixture depends on the vapor pressure, flash point, and handling temperature. Vapor pressures are divided into three categories: low, intermediate, and high.
Low-vapor-pressure products have a flash point greater than 100°F (38°C). Although these products do not develop flammable vapors under normal conditions, if they are contaminated with high-vapor-pressure materials or handled at temperatures above their flashpoints, ignition is possible. Examples of low-vapor-pressure products include kerosene, diesel fuel, Jet A aviation fuel, and safety solvents.
With a Reid vapor pressure below 4.5 pounds per square inch and a flashpoint below 100°F (38°C), intermediate-vapor-pressure products are flammable in the vapor space at ambient temperatures. Examples include Jet B aviation fuel and solvents like xylene, benzene, and toluene.
High-vapor-pressure products, such as motor and aviation gasoline, have a Reid vapor pressure above 4.5 pounds per square inch. Under normal handling conditions, these products produce a mixture too rich to be flammable in a restricted vapor space. However, a flammable mixture may still form and be present around an open vent during the transition to a rich mixture, which is potentially hazardous if there are any static sparks.
A condition for ignition also exists during switch loading. If a low-vapor-pressure product is loaded into a tank with flammable vapor from a previous load at or above the lower flammable limit, an explosion is possible. It is important to always consider the vapor pressure of the product being loaded, as well as the vapor pressure of the product carried on the previous load. Being aware of the vapor pressures can help reduce the risk of ignition during switch loading.
Static Control
Safety is a top priority for everyone involved in loading tank trucks with petroleum and other flammable products. By controlling the generation of static electricity, static discharge, and the vapor-air mixture at points where static can produce sparks, ignition potential can be eliminated. This is done in two ways: bonding and grounding.
Bonding is the process of connecting electrical bodies to provide a conductive path for static charges to flow. This eliminates the difference in electrical potential between two objects, which removes the spark gap.
Grounding serves a different purpose than bonding. Rather than equalizing electrical potential, grounding brings all parts of the system to the same zero ground potential. Since the tank truck and all its components have a different electrical potential than the ground, even when bonded, grounding provides a conductive path to the earth to eliminate the chance of a static spark.
Tank Truck Precautions
Even when a tank truck is properly bonded, static discharges can still occur when conditions are optimal for high rates of static electric generation and accumulation. Thus, additional precautions must be taken.
Relaxation Period
Microfilters and wire screens with a pore size of less than 150 microns can generate static charges. Providing a minimum of a 30-second relaxation period downstream of the filter or screen reduces the buildup of charges.
A tank gauging rod or sampling container projected into the cargo space of a tank truck can form a gap between itself and the rising liquid, creating a space for static sparks. To combat this, API recommends that tank truck operators wait 1 minute after filling has stopped before lowering conductive items into a compartment. This allows the charges to relax.
Limit Fill Velocity
Another precaution for tank truck loading is limiting fill velocity. The probability of static ignition can be reduced by restricting the flow rate to a maximum of 23 feet (7 meters) per second, or the value of v=0.5/d, whichever is less. In this equation, v is the velocity in meters per second and d is the inside diameter of the downspout in meters.
Tank Inspection
Tanks should always be inspected for unbonded conductive objects. A thorough safety inspection could be the difference between an uneventful load or combustion.
Top-Loading Tank Trucks
The type of loading system also plays a role in determining the necessary precautions. For top-loading tank trucks, a bond wire is required between the fill pipe and the tank truck before the dome cover is opened. All metal parts of the fill pipe should form a continuous, conductive path downstream from the point of bonding. The dome cover must be closed before the bond is removed.
Splash loading is another concern for generating electrostatic charges in top-loading trucks. When the fill pipe is only partially inserted into the cargo tank, the released liquid creates a splash effect on impact. This increased turbulence results in a high level of vapor generation, which is potentially dangerous in combination with static charges. Therefore, the fill pipe should be in contact with the bottom of the tank to avoid turbulence during loading. A T-deflector or 45-degree bevel should be used on the end of the downspout to prevent the pipe from resting flat on the bottom.
Bottom-Loading Tank Trucks
Bottom-loading tank trucks have additional precautions, as well. Internal tank shorting cables should be used in bottom-loading operations. In addition, during the initial stages of loading, upward spraying of the product can increase static generation. Reducing the fill velocity and using spray deflectors can help prevent a buildup of static charges.
Solutions from Dixon®
Dixon offers a variety of ground verification products to reduce the potential for static sparks and ultimately ignition while loading tank trucks.
Ground Verification Monitor (A240120)
Features:
- Bright red and green indicators communicate the A240 ground monitor status
- Convenient user terminal blocks make installation easy
- The environmentally sealed enclosure provides long service life even in outdoor environments
- Integrates easily into process control systems
- Provides and verifies ground bond through a single connection
Ground Clamp and Junction Box (A540CSB0251)
Features:
- The clamp is tethered to the cable by a stainless steel strap that protects the connection from strain and wear
- Pull-out resistant cord grip on junction box holds cable tighter the harder it is pulled
- The junction box creates a convenient service point for hazardous location installation
- Coiled cable provides compact storage
- Strong clamping force penetrates grime and remains connected during the loading process
- Provides ground and a ground-verification signal in a single clamp
Grounding Ball (GS1, GS2, GS1-2, FT451)
Features:
- Helps prevent static electric sparking when loading or unloading tankers containing flammable products
- The tanker is grounded using a groundline cable with a spring clip attached to a tank-mounted static grounding ball
Ground Wire (10735, FT452, FT452-002)
Features:
- Installed inside an API-compatible socket to provide verification of bonding between truck and load rack
Grounding Bolt (FT450)
Features:
- Helps prevent static electric sparking when loading or unloading tankers containing flammable products
- Part of a ground verification system when installed on API sockets and used with a Dixon FT7000 Rack Monitor
Top Loading T-Deflector (TLTD-300S, TLTD-400S)
Features:
- Minimizes splash and turbulence
- Even distribution of media to the sides of the tank, railcar, or tote
Conclusion
Loading and unloading tank trucks presents a serious hazard when static electricity is involved. Following relaxation periods, restricting flow velocity, understanding vapor pressure, and properly bonding and grounding tank trucks will keep operators safe and equipment on the road.
If this post sparked your interest, visit our transportation market page to learn more. You can also contact a Dixon specialist. Fire away with questions – we’re here to help!