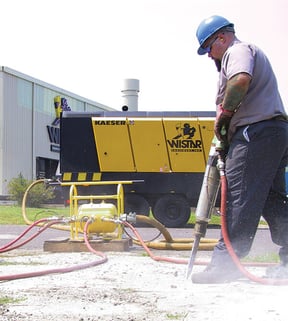
You are sitting in traffic and look over to see dusty air, roadwork signs, and power tools that sound like the roaring of a sold-out football stadium after a game-winning touchdown. You just drove past a construction site and all the equipment that inhabits it.
Have you ever looked at a massive jackhammer while sitting there and wondered, what in the world powers this monstrosity? Air! That’s right, air. Swinging a heavy sledgehammer and other repetitive, back-breaking tasks such as breaking up concrete or asphalt have been replaced with tools powered by compressed air. While extremely helpful when it comes to running heavy equipment, utilization of compressed air does not stop there. Across many trades, pneumatic tools (also known as air-powered tools) are used to replace what would usually be time-consuming, strenuous, manual tasks. These pneumatic tools include sanders, drills, chisels, saws, wrenches, and nail guns. The list goes on.
So, with all these high-pressured air tools there must be safety features to protect the operator, right? Yes, you are correct. Air is stored and expelled at great pressures to provide power to these tools. The Dixon team has engineered a diverse line of products to better protect those who utilize these tools daily.
Outside Air Safety Products:
Busy job sites typically require the simultaneous use of multiple pneumatic tools. This is where an air receiver manifold similar to the one pictured above comes into play. An air receiver manifold is used to store high-pressure air supplied from a compressor. The air from the compressor comes in through an inlet port and is expelled through the outlet ports allowing multiple pneumatic tools to be utilized at the same time without having to use multiple compressors to power them.
Dixon’s air receiver manifolds are certified by the American Society of Mechanical Engineers (ASME). What exactly does this mean? Our tanks are pressure tested to the regulated standard and certified by ASME. Our air receiver manifolds come with a tag welded onto the tank, this tag certifies that it is an ASME-certified pressure vessel. Occupational Safety and Health Administration (OSHA) can inspect the tank to ensure they are ASME certified.
One of the key components of an air receiver manifold is the Safety Check Valve (SCV-Series) pictured above. An SCV is a valve used in compressed air systems with hose connections. It prevents a hose from whipping in the event of a failure, which could result in serious injury or property damage. If your air hose has an inside diameter of more than a 1/2 inch, OSHA requires an SCV to be installed at the source of the air supply to shut off the air automatically in case of hose failure.
Some other common names for SCVs are:
• OSHA valves: OSHA Regulation 1926.302(b)(7) requires a device at the source of the air supply and at branch air supply line
• Fuses for air hoses: Too much current blows a fuse and too much airflow shuts off an internal valve in the SCV
• Excess flow valves: They stop “excess flow” from entering the hose
Compressed air is supplied through hoses to power pneumatic tools and equipment. The SCV is installed upstream of the hose to prevent it from whipping in the event of a hose or coupling failure. As the airflow increases through the SCV, the valve begins to compress the spring. If the airflow of the tool is greater than the SCV rating, the valve will close until it meets the seal and the airflow is cut off.
To learn more about SCVs, please visit our previous blog post on this product!
If a safety check valve is not being used, OSHA requires a safety cable, such as Dixon’s King safety cable pictured above to be attached to the hose.
King safety cables prevent hose whip in the event of the accidental separation of a coupling or clamp device. The steel cables span the hose fittings to provide standby safety for the hose. Spring-loaded loops in the cable ends are easily opened to pass over the couplings and provide a firm grip on the hose. On hose-to-hose applications, the King safety cable should be installed on the hose portion of the assembly in a fully extended position. When used on a hose-to-rigid outlet, or tool, the spring-loaded end should be over the hose, while the choker end is installed on the outlet or tool. We also recommend a King safety cable at all "hose-to-hose" or "hose-to-tool" connections, regardless of the use of a safety check valve.
Our King safety cables are commonly found on many job sites. They are available in carbon steel and stainless steel, depending on the environment in which they will be used, and should always be installed in a fully extended position.
To learn more about King safety cables, please visit our previous blog post on this product!
Our King Safety Whipsocks are ideal for applications that utilize higher pressures (maximum working pressure ranges from 250 to 5000 PSI, depending on size) including air, water, slurry, and even hydraulic applications. They feature dual anchor points to eliminate hose whip in the event of a disconnection. The woven stockings extend down the hose to grip securely over a larger area. Securing them eye-to-eye in a hose-to-hose connection or eye-to-rigid / fixed point reduces hose whip in the event of a failure or accidental disconnect. Used with King Safety Whipsocks, King Safety Shackles anchor the whip socks (we recommend the use of bolt, nut, and cotter pin style shackles).
At Dixon, we are committed to educating our customers about the broad range of products we manufacture and distribute. We hope this post provided helpful insight on our outside air products, and how Dixon can help with solutions for your individual applications. If you enjoyed this blog post, please share it with your friends and colleagues!
Click here for additional information on our Outside Air products.
If you would like to speak with a Dixon specialist, please call 877.963.4966 or visit dixonvalve.com