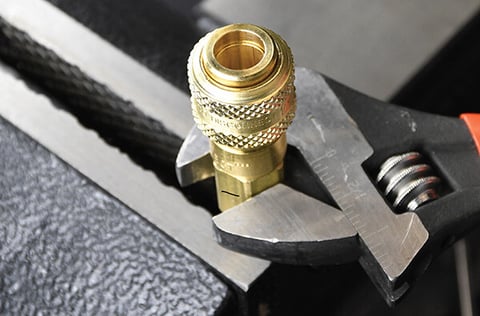
History
The onset of the industrial revolution increased the need for the standardization of screw threads. As new manufacturing processes emerged it became obvious just how many different types of threads existed. This caused compatibility issues between different manufacturers and users.
In 1841, Sir Joseph Whitworth, an English engineer and inventor created a uniform threading system to address the issue. His thread form was based on a 55-degree thread angle with rounded roots and crests. This became a widely accepted standard for connecting thread for pipes and became known as the British Standard Pipe thread (BSP).
BSP threads were often used in the United States and Canada through the 1860s, but they were never universally accepted, so the lack of compatibility and need for standardization remained. In 1864, William Sellers, an American engineer, proposed a new set of standards for bolts, screws, and nuts. His design featured a 60-degree angle with flattened peaks and valleys that was easier to manufacture and produce. Sellers’ design, known as National Pipe Tapered (NPT) threads, gained widespread acceptance and played a vital role in the American industrial revolution. NPT threads were eventually adopted as the national standard in the U.S.
NPT and NPTF Threads
As indicated in the name, NPT threads are tapered, which means the threads decrease in diameter over the length of the threads. This differs from parallel or straight threads where the diameter stays the same. Additionally, tapered threads can create a seal on their own, whereas straight threads hold the connection together but require a gasket or O-ring for sealing.
To dive deeper into the basics of threads, check out this blog post: Threads 101.
It is important not to confuse NPT threads with NPTF threads. NPTF stands for National Pipe Taper Fuel. While NPT and NPTF threads are identical in appearance, the way they create leak-resistant seals is different.
There is a slight clearance between the roots and crests of NPT threads. This creates a spiral leak path along the male thread crests. A thread sealant is required to prevent leaks. NPTF threads, however, do not require a sealant.
Paste or PTFE tape can be used as a sealant. The type of PTFE tape depends on the application. Dixon offers the following types of PTFE tape:
● Industrial Heavy Duty PTFE tape
● Industrial PTFE tape
● Stainless steel PTFE tape
● PTFE tape for LP gas
● American Made PTFE tape
Safety note: These PTFE tapes are not intended for use in oxygen applications.
How to Use PTFE Tape
The seal on NPT threads is created by the metal-to-metal contact between the roots and crests of the male and female threads. Using too much PTFE tape or pairing liquid sealant with PTFE tape may cause distortion, poor thread engagement, or cracking of the coupling during assembly.
The total number of threads engaged should be between 3-1/2 to 6. Any number of threads outside of this range may indicate over or under-tightening, or out-of-tolerance threads.
Step 1: Apply 1-1/2 to 2 wraps of PTFE tape, starting one or two threads from the lead edge, in a clockwise direction.
Step 2: Check threads to ensure there is no obvious damage on either half and the tape is properly installed. Align male and female threaded connections and carefully begin threading the two halves together.
Step 3: Finger-tighten the connection and create a reference mark on the hex of the hose end/adapter of the coupling. This mark will help identify the number of revolutions during the next step in the procedure.
Step 4: Using an even and smooth force, tighten the connection with a wrench according to the turns from finger tight (TFFT) values listed in the table. Do not over-tighten.
After assembling an NPT thread connection, always proof-test the connection before operating the system. This is done by pressurizing the unit to 150% of the working pressure in an enclosed/protective environment. If the joint proved to be inadequately tightened during proof-pressure testing, tighten it further in 1/8 turn increments until a reliable seal is attained. Do not exceed 3 turns from finger tight.
Safety
All couplings should be viewed as potential hazards that can cause property damage, personal injury, or even death if used or installed improperly. Improper use includes selecting a product unsuitable for your application, installing or using the product incorrectly, and/or ignoring signs of imminent failure or misuse. Failure may result in explosive propulsion of components, rapid expulsion of hazardous media, and failure or unintentional movement of a fluid-powered component.
Couplings should be installed in a location that will allow easy operation of the coupling and accessibility for all necessary installation tools. Care should be given to consider operator safety, especially if spillage upon disconnect could result in fluid ignition or skin and eye irritation.
Only apply wrenches to the hex or machined wrench flats that are provided for assembly purposes, nowhere else. Never clamp on the sleeve of the coupler or the nose of the plug as this will cause distortion and/or damage.
Dixon Quick Coupling
Dixon Quick Coupling, located in Dallas, North Carolina, manufactures and supplies a diverse range of hydraulic and pneumatic quick disconnect couplings including HT-AG series adapters, high-pressure TD-series fittings, and the Correct Connect®. The parts offered by Dixon Quick Coupling feature NPT and other thread types suitable for a wide variety of applications.
Dixon Brass
In addition, Dixon Brass, located in Westmont, Illinois, manufactures and supplies a variety of products such as brass ferrules, welding connectors, pipe, push-on, compression, and DOT airbrake fittings. These parts also feature NPT and NPTF threads to ensure you always have The Right Connection®.
For More Information
Along with a variety of other interactive tools, Dixon’s product cross-reference tool is available online and compatible with both mobile devices and computers. Simply enter a part number and click search to cross-reference it with the Dixon product line.
Want to learn more? Visit dixonvalve.com or contact Dixon Quick Coupling at 800.839.9022 or Dixon Brass at 800.323.4440.